Scoby Textiles part 2
- Jonathan Pereira
- May 29, 2019
- 4 min read
Updated: Jan 30, 2021
If you’ve been following our social media, you’ve seen periodic updates of Eva’s SCOBY textile project. Below is her summary, the final product, and thoughts on where to go next with flexible materials made from these single-celled organisms.
As discussed in my initial blog post, I focused on two experimental paths: the brewing of kombucha specifically for harvesting SCOBY, and the post-harvest processing on existing leftover SCOBY. I will continue to refer to the SCOBY (Symbiotic Culture Of Bacteria and Yeast) as bacterial cellulose, or ‘BC’ because it more accurately describes what it is in a material context.
After finishing experiments in both of these paths, I had more success with post-harvest processing on existing leftover bacterial cellulose than growing BC exclusively for that purpose. I believe this is because we grew the material in an environment which was not optimal for a thicker sheet of BC, and the post-harvest processing was done on BC grown under different environmental conditions. Arize Kombucha provided this SCOBY, which achieved a hefty thickness. There are many factors that could contribute to thicker growth in the future, including the addition of more sugar and increasing the temperature from 80 °F to around body temperature, (mid to upper 90 degrees Fahrenheit.) The physical setup could remain the same, and is shown below.


Below are photos of two sheets of BC that grew for 4 weeks, which measured about 5 mm in thickness before drying, in comparison to pieces formed from the material which was provided by Arize Kombucha (1-2 cm thick before drying). The opacity of these two types shows their different thicknesses as well.
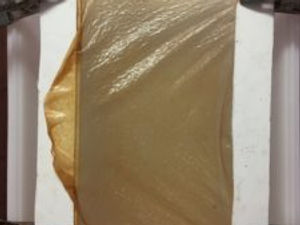



Generally, the most successful materials arose from using post-harvest ‘waste’ BC and grinding it up in a food processor, then drying it. As I mentioned above, the post-harvest waste product BC was thicker overall. It was also more abundant than the material we grew, so I chose to use it for many different ‘grind-up and dry’ tests. The experiments that resulted in my most successful materials were when I:
Put some BC in a food processor, ground it up. Spread it out in 4 spreads and applied ~1 tbsp of oil (coconut oil mixture or tung oil) Placed the 4 spreads either in an oven to dry, then remove them and air dried them, or dried them in a food dehydrator. These resulted in the strongest and most flexible materials.
The photo below addresses my 4 most successful experiments with this general outline:
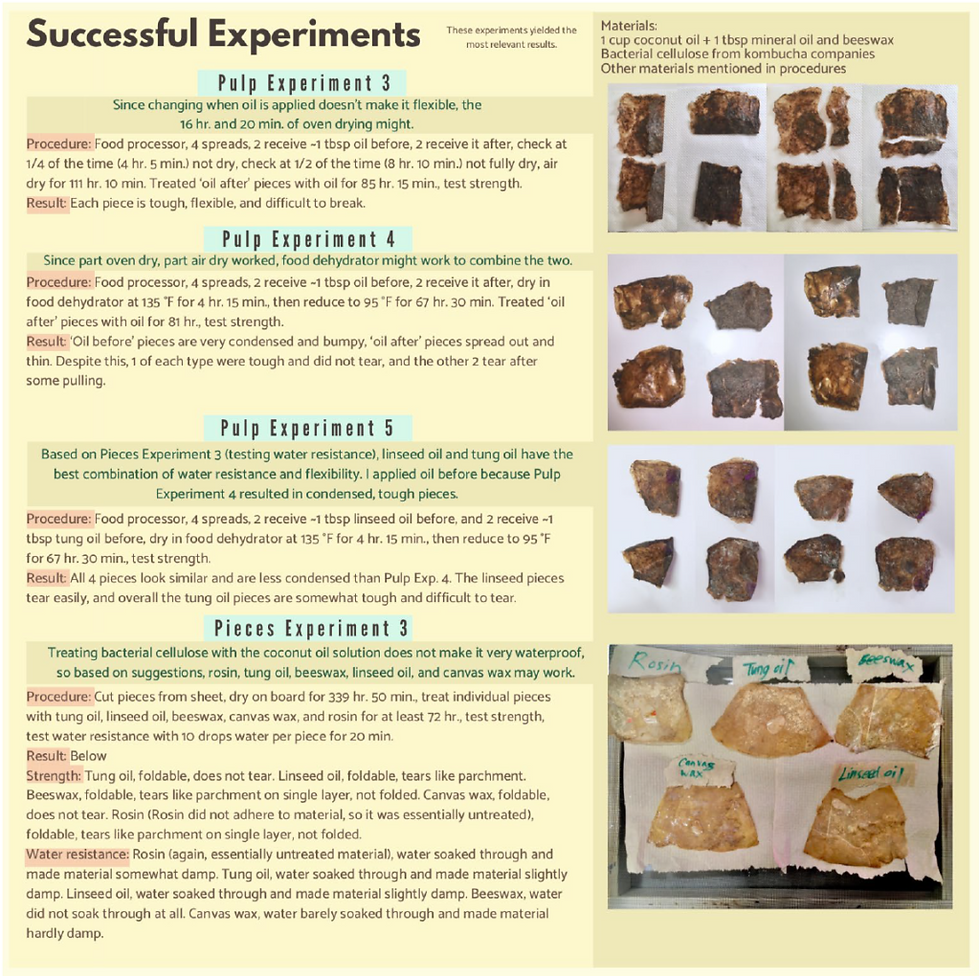
Successful attempts in evaluating bacterial cellulose post-processing
Conclusions
Even with the previous statements regarding use as a leather-like textile, the most realistic use would be packaging or disposable plates. Many of the results that I got earlier I view as unsuccessful because they were much too thin and breakable with constant movement. Though they aren’t ideal for my intended purpose as a textile, these characteristics would work well for a single-use plastic replacement for goods such as cosmetics packaging (which someone has actually done1) or dry food, along with disposable plates (someone has also done this2). I originally intended this to resemble thin leather, because many of my sources and references used the material for that purpose (3, 4, 5, 6, 7, 8, 9). I have managed to make a material that will work, and have made a wallet out of it.
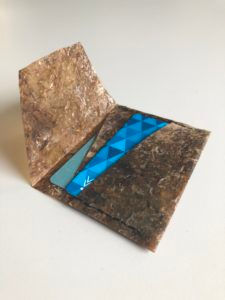
This particular material is one of the most successful pulp-based ones: applying ~1 tbsp of tung oil to BC pulp and drying it in a food dehydrator. Even so, after further consideration, though this material is more water resistant than the materials treated with the coconut oil solution, the texture is not ideal as it is potentially too thin. A more ideal material would be partially taking from Pulp Experiment 4 above where I treated the pulp with the coconut oil solution prior to drying, then treating it with tung oil. This would provide a thicker and potentially more durable wallet.
Next steps
Here are some next steps if someone were to carry this project on:
Attempt to grow thicker BC by adding more sugar to the solution and increasing the room’s temperature. Or adding additional sugar during the growing process (sugar rich waste products such as those from candy production could even be considered). Explore creating this material into disposable packaging and plates. You could also use thinner material as an alternative to thin plastic packaging.
If anyone would like to explore any of these future possibilities, please let us know!
References
Elena Amato — Hitti, Natashah. “Elena Amato Creates Sustainable Cosmetics Packaging from Bacteria.” Dezeen, Dezeen, 28 Feb. 2019, www.dezeen.com/2019/02/28/elena-amato- bacteria-packaging-design/.
Emma Sicher — Hitti, Natashah. “Emma Sicher Makes Eco-Friendly Food Packaging from Fermented Bacteria and Yeast.” Dezeen, Dezeen, 15 Nov. 2018, www.dezeen.com/2018/11/13/sustainable-food- packaging-emma-sicher-peel/.
Scihouse. How to Grow Leather-like Material Using Bacteria (Making Kombucha Leather). YouTube, Scihouse, 1 May 2017, www.youtube.com/watch?v=Ds8ZFzOwGeI.
“Grow Your Own Clothes.” Performance by Suzanne Lee, TED, TED, 2011, www.ted.com/talks/suzanne_lee_grow_your_own_clothes/up-next.
Quijano, Luis. “Embracing Bacterial Cellulose as a Catalyst for Sustainable Fashion.” Liberty University, ResearchGate, 2017, pp. 4–30. ResearchGate, www.researchgate.net/publication/322498822_Embracing_Bacterial_Cellulose_as_a_Catalyst_for_Sustainable_Fashion_Senior_Honors_Thesis.
Sarubbo, Leonie. “Review- Bacterial Cellulose: An Ecofriendly Biotextile.” Universidade Católica de Pernambuco, ResearchGate, 2017, pp. 11–21. ResearchGate, www.researchgate.net/publication/314234769_REVIEW_- BACTERIAL_CELLULOSE_AN_ECOFRIENDLY_BIOTEXTILE.
Sulaeva, Irina, et al. “Bacterial Cellulose as a Material for Wound Treatment: Properties and Modifications: A Review.” University of Natural Resources and Life Sciences, ScienceDirect, 2015, pp. 1548–1566.
Sumanasinghe, Ruwan D., and Martin W. King. “New Trends in Biotextiles – The Challenge of Tissue Engineering.” Journal of Textile and Apparel, Technology and Management, College of Textiles, North Carolina State University, vol. 3, no. 2, 2003, pp. 2–12. NC State University, textiles.ncsu.edu/tatm/wp-content/uploads/sites/4/2017/11/sumana_full_62_03.pdf.
Zöhrer, Pedro. “Kombucha Wallet.” Instructables, Instructables, 17 Aug. 2017, www.instructables.com/id/Kombucha-Wallet/.